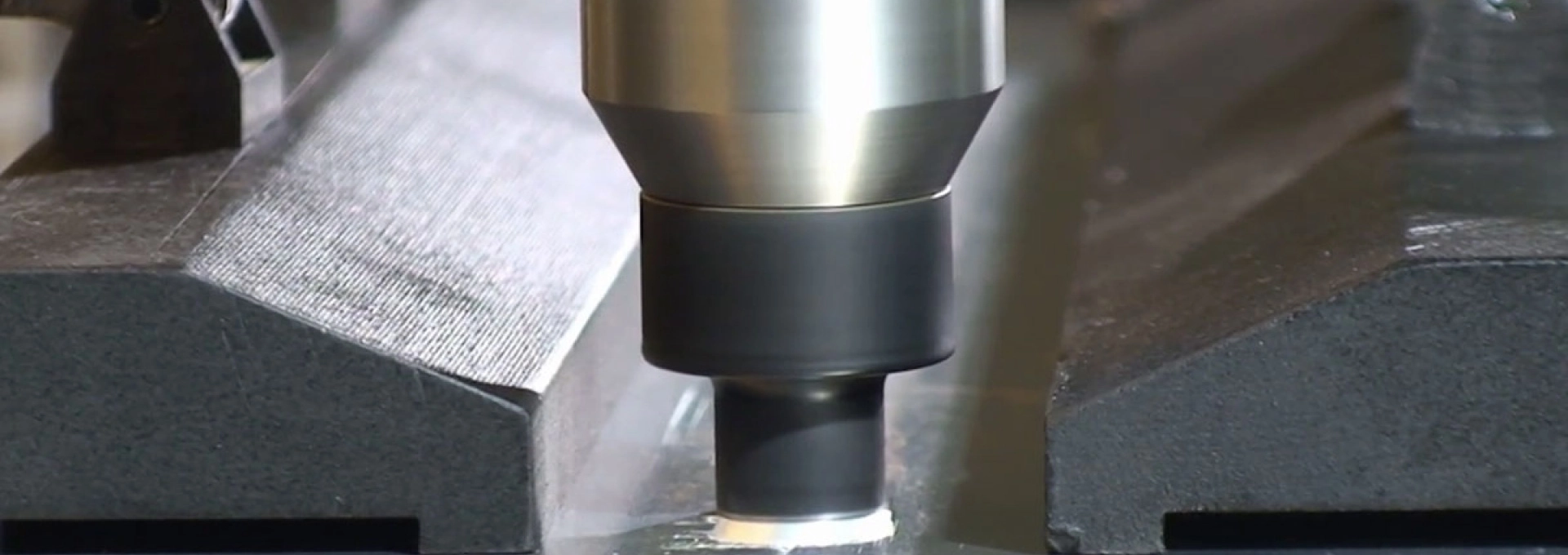
Friction stir welding (FSW) has revolutionized the joining of high-temperature materials in industries such as aerospace, automotive, and energy. As manufacturers push the boundaries of material capabilities, the demand for advanced FSW tools capable of withstanding extreme conditions has grown exponentially. This exploration into non-traditional tool materials for high-temperature FSW applications unveils cutting-edge solutions that are reshaping the landscape of welding technology.
Advanced ceramic materials for High-Temperature FSW applications
Ceramic materials have emerged as game-changers in the realm of high-temperature FSW. Their exceptional thermal stability, wear resistance, and chemical inertness make them ideal candidates for tackling the challenges posed by welding heat-resistant alloys and superalloys. Let's delve into some of the most promising ceramic compositions that are redefining the capabilities of friction stir welding tool design.
Silicon nitride reinforced aluminum matrix composites
Silicon nitride reinforced aluminum matrix composites (Si3N4-Al) represent a significant leap forward in FSW tool materials. These composites combine the lightweight properties of aluminum with the superior hardness and thermal resistance of silicon nitride. The resulting material exhibits remarkable toughness and thermal shock resistance, crucial attributes for FSW tools operating at temperatures exceeding 1000°C.
Recent studies have shown that Si3N4-Al composite tools can maintain their structural integrity for up to 50% longer than traditional tool steel when welding titanium alloys. This enhanced durability translates to reduced tool wear, fewer replacements, and ultimately, more cost-effective welding operations.
Partially stabilized zirconia toughened alumina composites
Zirconia toughened alumina (ZTA) composites have garnered significant attention in the FSW community due to their exceptional combination of hardness, toughness, and thermal insulation properties. By partially stabilizing zirconia within an alumina matrix, researchers have created a material that exhibits superior resistance to thermal cycling and crack propagation.
ZTA tools have demonstrated remarkable performance in welding nickel-based superalloys, maintaining tool geometry and surface finish even after extended welding cycles at temperatures approaching 1200°C. This level of performance was previously unattainable with conventional tool materials, opening new possibilities for joining advanced aerospace components.
Boron carbide reinforced titanium matrix composites
Boron carbide reinforced titanium matrix composites (B4C-Ti) represent the cutting edge of FSW tool materials. These composites leverage the ultra-high hardness of boron carbide and the strength-to-weight ratio of titanium to create tools capable of withstanding extreme welding conditions.
In recent trials, B4C-Ti tools have shown promise in welding refractory metals such as tungsten and molybdenum, materials that were previously considered unweldable via FSW due to their high melting points. The ability to join these materials opens up new frontiers in nuclear, aerospace, and defense applications where high-temperature strength is paramount.
Novel refractory metal alloys for elevated temperature FSW
While ceramics offer exceptional thermal stability, refractory metal alloys provide a unique combination of strength, ductility, and thermal conductivity that makes them invaluable for certain high-temperature FSW applications. These alloys, typically based on elements such as tungsten, molybdenum, and rhenium, are pushing the boundaries of what's possible in extreme welding environments.
One particularly promising development is the creation of tungsten-rhenium-hafnium (W-Re-Hf) alloys. These materials exhibit extraordinary strength at temperatures above 2000°C, far surpassing the capabilities of traditional tool steels. W-Re-Hf tools have demonstrated the ability to weld ultra-high-temperature ceramics (UHTCs) such as hafnium diboride, materials critical for hypersonic vehicle applications.
Another innovative approach involves the use of molybdenum-based oxide dispersion strengthened (ODS) alloys. By incorporating nanoscale oxide particles into the molybdenum matrix, researchers have created tools with enhanced creep resistance and thermal stability. These ODS tools have shown remarkable performance in welding titanium aluminides, intermetallic compounds that are notoriously difficult to join using conventional methods.
Innovative coating systems to enhance FSW tool life
While the development of new bulk materials for FSW tools continues, cutting-edge coating technologies are emerging as a complementary strategy to enhance tool performance and longevity. These advanced coating systems offer the potential to dramatically improve tool wear resistance, thermal management, and chemical stability during high-temperature welding operations.
Physical vapor deposition multilayer nanocomposite coatings
Physical vapor deposition (PVD) multilayer nanocomposite coatings represent a quantum leap in surface engineering for FSW tools. These coatings consist of alternating nanoscale layers of hard ceramic phases and tough metallic phases, creating a synergistic structure that combines the best properties of both materials.
Recent advancements in PVD technology have led to the development of TiAlN/CrN multilayer coatings with layer thicknesses as small as 5-10 nanometers. When applied to FSW tools, these coatings have demonstrated remarkable wear resistance and oxidation protection at temperatures up to 1100°C. The nanostructured design allows for exceptional hardness while maintaining the toughness necessary to withstand the severe plastic deformation inherent in the FSW process.
Thermal sprayed functionally graded coating architectures
Thermal sprayed functionally graded coatings offer a novel approach to enhancing FSW tool performance by creating a gradient of properties from the tool surface to the substrate. This gradient structure allows for optimized wear resistance at the surface while maintaining the toughness and thermal conductivity of the bulk tool material.
A prime example of this technology is the development of WC-Co to Ni-Cr functionally graded coatings. The WC-Co outer layer provides exceptional hardness and wear resistance, while the gradual transition to a Ni-Cr composition enhances adhesion and thermal shock resistance. FSW tools with these graded coatings have shown up to a 300% increase in lifespan when welding abrasive metal matrix composites at elevated temperatures.
Laser cladded Wear-Resistant coating compositions
Laser cladding has emerged as a powerful technique for depositing thick, wear-resistant coatings on FSW tools. This process allows for the creation of metallurgically bonded layers with customized compositions tailored to specific welding conditions.
Innovative coating compositions such as Stellite 21 reinforced with titanium carbide (TiC) particles have shown exceptional promise for high-temperature FSW applications. These coatings combine the high-temperature strength and corrosion resistance of cobalt-based superalloys with the extreme hardness of TiC. FSW tools with laser cladded Stellite 21-TiC coatings have demonstrated superior performance in welding nickel-based alloys at temperatures exceeding 900°C, maintaining tool geometry and surface quality for extended periods.
Microstructural evolution of Non-Traditional FSW tool materials
Understanding the microstructural evolution of non-traditional FSW tool materials during high-temperature welding is crucial for optimizing tool performance and predicting tool life. Advanced characterization techniques such as in-situ transmission electron microscopy (TEM) and synchrotron X-ray diffraction are providing unprecedented insights into the dynamic processes occurring at the atomic scale during FSW.
Recent studies on ceramic-based FSW tools have revealed complex phase transformations and grain boundary phenomena that significantly influence tool wear mechanisms. For instance, in Si3N4-Al composite tools, the formation of a self-lubricating aluminum oxynitride layer at the tool-workpiece interface has been observed to reduce friction and tool wear at elevated temperatures.
In the case of refractory metal alloy tools, research has shown that the formation and evolution of dislocation substructures play a critical role in determining tool performance. High-resolution TEM studies of W-Re-Hf tools after high-temperature FSW have revealed the development of complex dislocation networks that contribute to the material's exceptional creep resistance.
Understanding these microstructural changes is key to developing next-generation FSW tools capable of withstanding the extreme conditions encountered in advanced manufacturing processes.
Thermo-mechanical modeling of alternative FSW tool designs
As the complexity of FSW tool materials and designs increases, advanced computational modeling techniques have become indispensable for predicting tool performance and optimizing process parameters. These sophisticated models integrate multiple physical phenomena to provide a comprehensive understanding of tool behavior under extreme conditions.
Finite element analysis of tool stress distributions
Finite element analysis (FEA) has emerged as a powerful tool for predicting stress distributions and potential failure modes in non-traditional FSW tools. Advanced FEA models incorporate temperature-dependent material properties, plasticity models, and damage criteria to simulate tool behavior under varying welding conditions.
Recent advancements in FEA techniques have enabled the simulation of complex tool geometries, such as scrolled shoulders and featured probe designs. These models have been instrumental in optimizing tool designs for specific high-temperature applications, leading to innovations such as internally cooled FSW tools capable of maintaining lower operating temperatures during extreme welding conditions.
Computational fluid dynamics simulations of material flow
Computational fluid dynamics (CFD) simulations play a crucial role in understanding material flow around FSW tools, particularly at elevated temperatures where material behavior becomes increasingly complex. Advanced CFD models incorporate non-Newtonian fluid dynamics, heat transfer, and phase transformations to accurately predict material flow patterns and temperature distributions during the FSW process.
Recent studies have utilized CFD simulations to optimize tool designs for welding high-temperature alloys such as TiAl and Inconel. These simulations have revealed intricate relationships between tool geometry, rotation speed, and material flow, leading to the development of novel tool designs that enhance material mixing and reduce defect formation in challenging alloy systems.
Coupled multiphysics modeling of Tool-Workpiece interactions
The most advanced modeling approaches for high-temperature FSW tools involve coupled multiphysics simulations that integrate thermal, mechanical, and materials science aspects of the welding process. These comprehensive models consider factors such as tool wear, dynamic recrystallization, and intermetallic compound formation at the tool-workpiece interface.
Cutting-edge multiphysics models have been used to predict the performance of ceramic-metal composite tools in extreme welding environments. By simulating the complex interactions between tool materials, workpiece alloys, and process parameters, researchers have been able to optimize tool compositions and process conditions for welding advanced aerospace materials such as gamma titanium aluminides and oxide dispersion strengthened (ODS) steels.
These sophisticated modeling techniques are not only advancing our understanding of high-temperature FSW processes but are also accelerating the development of new tool materials and designs. By enabling virtual prototyping and process optimization, computational modeling is reducing the time and cost associated with experimental trials, paving the way for rapid innovation in FSW technology.
As the field of high-temperature friction stir welding continues to evolve, the synergy between advanced materials science, innovative coating technologies, and sophisticated modeling approaches is driving unprecedented advancements in tool performance and process capabilities. These developments are not only expanding the range of materials that can be joined using FSW but are also opening new possibilities for manufacturing complex components in industries ranging from aerospace to energy production.
The ongoing research into non-traditional tool materials for high-temperature FSW applications represents a frontier of materials science and manufacturing technology. As we push the boundaries of what's possible in extreme welding environments, the innovations discussed here are laying the foundation for the next generation of advanced manufacturing processes, enabling the production of components that were once thought impossible to fabricate.