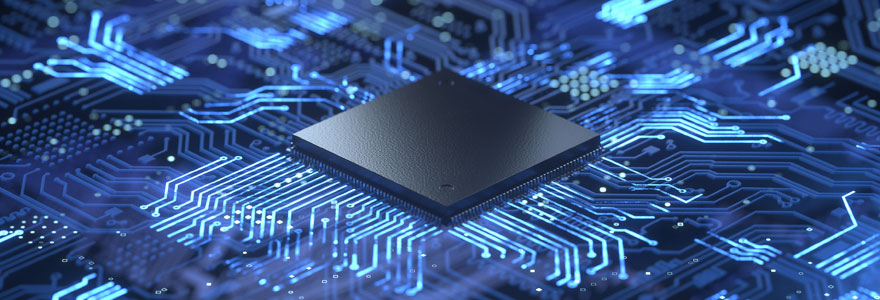
The digitization of appliances and automobiles has seen semiconductors used on almost any electronic equipment. These chips process digital inputs to enable the equipment to do its work. The complex parts require several processes to produce and test them to be ready to work on the appliances for which they were designed. Different equipment is used in the semiconductor manufacturing processes, depending on the stage. Exchange your PRI Robotics pre align with the latest machines at discounted prices.
The four stages of production include wafer fabrication, assembly, testing and packaging. Here are the main machines. You may exchange your PRI Robotics pre aligner for speed and quality performance with upgraded ones.
Wafer Fabrication Equipment
The epitaxial deposition equipment is used in the fabrication of semiconductor wafers. This equipment includes oxidation systems, diffusion systems and ion implantation equipment. Other equipment includes physical and chemical vapour deposition systems. A basic reactor contains a reactor tube that isolates the epitaxial environment and another one that distributes chemicals for deposition in the chemical environment. It also includes a system for heating the wafers and removing the effluent gases. The repair of pre-aligners made by PRI Robotics is fast and effective.
After deposition, a photolithography machine creates circuits on the wafer while etching equipment removes extra materials from the surface. The manufacturers require preventive maintenance for PRI Robotics pre-aligners used to deliver the parts to the required systems.
Wafer Assembly Equipment
Die attach machines mount the die to the die pad during the wafer assembly process. They have systems to hold and index lead-frames on which a die is mounted. Then, a wirebonder connects the die of the device electrically to the leads.
The chip is taken to the moulding equipment, where the integrated circuits are encapsulated. The machine includes a preheating chamber that incorporates a melting pot, several runners, and moulding cavities. After encapsulation, wafers go to deflash machines.
The machines then trim, form, and singulate the IC packages. A single machine may have all these components, but there are dedicated ones for each process. These are automated punches, anvils, and blades that automatically assemble and polish the chips into the right dimensions. Regular PRI Robotics maintenance is vital for this equipment.
Finally, the chips go through solder plating machines, which apply a lead finish to semiconductors. The machines subject chips to electrochemical processes that deposit metal layers on the product for plating.
Semiconductor Test Equipment
Chip companies use automatic test equipment (ATE) to check the electrical characteristics and performance of the ICs. These tools vary according to the type of semiconductor they are testing. However, all of them come with a microprocessor or controller that controls the entire process, modules that supply electrical charges across the circuit, and modules that measure the characteristics of the device under test in response to the charge that was passed.
Depending on the semiconductor under survey, there can be additional systems attached to the ATE to enable the system to measure specific characteristics of the IC, as most testers are generic. In huge production facilities, ATES have test handlers that present the ICs to the test site and remove them when the process is complete. This makes the entire testing process fast and effective. These handlers also sort the chips according to the results of the tests. You may exchange your PRI Robotics pre-aligners for better systems for enhanced productivity.
Sealing and Packaging
Once the chips have passed the test section, they are now packed and sealed, ready for transport. The chips are placed in the carrier tape pockets, and then the tape is rolled onto a reel. Taping and reeling are alternatives for semiconductors that cannot be shipped in tubes. The automatic tube loading mechanism is the first step of the process, and some chips are not placed in pockets.
You should have preventive maintenance for PRI Robotics pre-aligners to ensure that the entire manufacturing process does not slow down. It also saves you from more expensive repair services for PRI Robotics that may also take a long time to complete.